
Hitachi Astemo
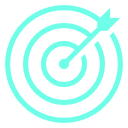
Goal
Improve material availability to production lines, reduce inventory

Plan
Training for vendors, buffer management put in place, plant team, supply chain management team
Problems Identified
Sales loss at dealer level or OEM/OES
Lack of availability at warehouses
Loss of production/capacity
High Expediting Cost/Premium Freight
Shortages at the assemblies
High Expediting Cost/Premium Freight
High Stress level
Solutions Provided
Improved availability at the child part level
Going from Push/Forecast based to Pull
Decoupled the plant from market and suppliers from the plant
Buffer building at RM level, Assembly level and plant level to absorb demand and supply variation
Putting single priority system throughout the organisation
Improved coordination between planning and production
Results
- The inventory was reduced by 5 days. This resulted in huge cost-saving, which in turn translates to an increase in company profits. If the inventory time is longer, a lot of additional costs get added, making the process inefficient, and cost-ineffective. By changing the approach of production from push-based to pull-based, they were able to control and deliver optimum productivity, without losses or excess costs involved.
- Many times a supply chain desired material is not available on time which creates unnecessary delays in production, delivery, and ultimately affects the profit margins of the companies. Hitachi Astemo could substantially improve on-time delivery of components thereby resulting in faster and more efficient operations. By decoupling the plant from the market and suppliers from the plant, the company could ensure that components are delivered on-demand, and on time.
Along with these two major results, the overall performance parameters reflected growth and end to end system management approach helped in sustained positive profit levels.
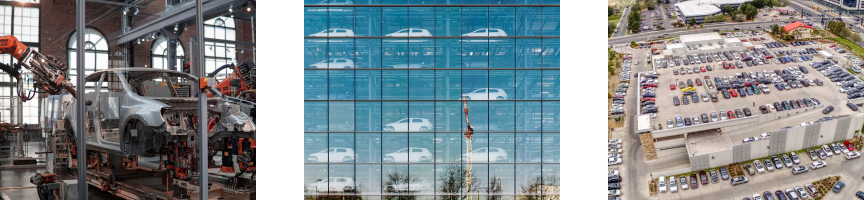
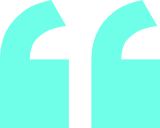